-
Telephone:+0086-371-6376-8262Telephone:+0086-371-6376-8385
-
wechat:abcdefg
-
-
Email:ht@ovenfurnace.com
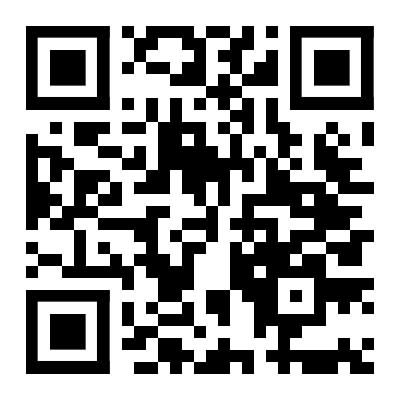
First, water cooling device, vacuum heat treatment furnace shell, furnace cover, electric heating element conduction treatment (water-cooled electrode), intermediate vacuum insulation and other components, all work under vacuum and heat. Working under such extremely unfavorable conditions, it is necessary to ensure that the structure of each component is not deformed, not damaged, and the vacuum seal ring is not overheated and not burned. Therefore, each component should be equipped with a water cooling device according to different conditions to ensure that the vacuum heat treatment furnace can operate normally and have enough service life.
Second, the use of low voltage and high current: in the vacuum container, when the true emptiness is within the range of several to one lxlo-1, the energized conductor in the vacuum container will produce glow discharge at a higher voltage. In the vacuum heat treatment furnace, serious arc discharge will be generated, burning the electric heating element, insulation layer, etc., resulting in major accidents and losses. Therefore, the operating voltage of the electric heating element of the vacuum heat treatment furnace is generally not more than 80 to 100 volts. At the same time, effective measures should be taken when designing the structure of the electric heating element, such as avoiding parts with tips as far as possible, and the spacing between the electrodes should not be too narrow to prevent the occurrence of glow discharge or arc discharge.
Third, most of the heating and insulation materials can only be used in the vacuum state: the heating and insulation lining of the vacuum heat treatment furnace is working under vacuum and high temperature, so these materials put forward high temperature resistance, low steam pressure, good radiation effect, small thermal conductivity and other requirements. Anti-oxidation performance requirements are not high. Therefore, tantalum, tungsten, molybdenum and graphite are widely used as heating and heat insulation materials in vacuum heat treatment furnaces. These materials are easily oxidized in the atmosphere, so these heating and insulation materials cannot be used in conventional heat treatment furnaces.
Fourth, strict vacuum seal: It is well known that vacuum heat treatment of metal parts is carried out in a closed vacuum furnace, therefore, to obtain and maintain the original leakage rate of the furnace, to ensure the working vacuum of the vacuum furnace, to ensure the quality of the vacuum heat treatment of parts has a very important significance. Therefore, a key problem of vacuum heat treatment furnace is to have a reliable vacuum seal structure. In order to ensure the vacuum performance of the vacuum furnace, a basic principle must be followed in the structure design of the vacuum heat treatment furnace, that is, the furnace body should be air-tight welding, while the furnace body should be less open or not open holes, and the dynamic seal structure should be less used or avoided to minimize the chance of vacuum leakage. The components and accessories installed on the vacuum furnace body, such as water-cooled electrodes and thermocouple export devices, must also be designed to seal the structure.
High degree of automation: The high degree of automation of vacuum heat treatment furnace is because the heating, cooling and other operations of metal workpieces require a dozen or even dozens of actions to complete. These actions are carried out inside the vacuum heat treatment furnace and cannot be approached by the operator. At the same time, some actions such as heating and insulation after the end of the metal workpiece quenching process must be six actions and to be completed within 15 seconds. In such a rapid condition to complete many actions, it is easy to cause the operator tension and constitute misoperation. Therefore, only higher automation can accurately and timely start according to the program coordination.
New Sapphire Vacuum Crystal Growth Furnace Bolsters Scientific Research and Industry Development
Innovative glove box induction melting system with gas purification function (1ppm) to assist high-purity production
Product: Automatic Recirculating Gas Purification System (O2 < 1 ppm) With Temperature Control System
Innovative technology leads to creating ultra pure environment - Automatic Recirculating Gas Purification System (O2 & H2O < 1 ppm) For Glovebox makes a stunning debut